Yield Definition In Manufacturing
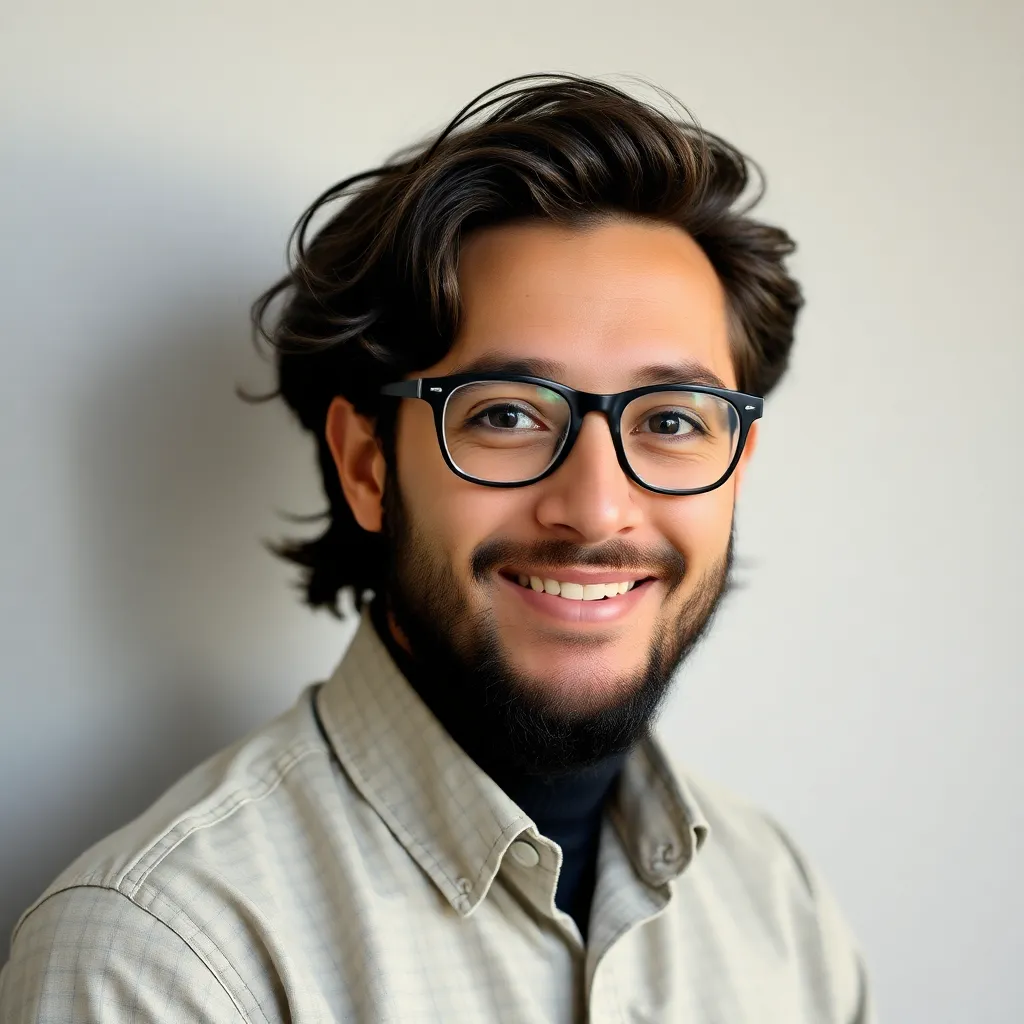
adminse
Mar 29, 2025 · 9 min read
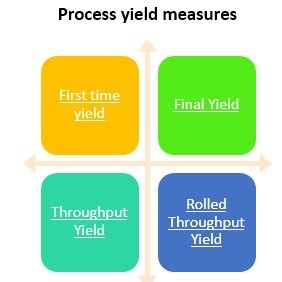
Table of Contents
Understanding Yield in Manufacturing: A Comprehensive Guide
What truly defines yield in the complex world of manufacturing, and why does it matter so significantly?
Yield is the ultimate indicator of manufacturing efficiency, directly impacting profitability and competitiveness.
Editor’s Note: This comprehensive guide to yield definition in manufacturing was published today, offering the latest insights and best practices for optimizing production processes.
Why Yield Matters in Manufacturing
Yield, in its simplest form, represents the ratio of good output to total input in a manufacturing process. However, its significance extends far beyond a simple numerical value. A high yield signifies efficient resource utilization, reduced waste, and ultimately, increased profitability. Conversely, low yield indicates inefficiencies, leading to increased costs, lost revenue, and potentially, competitive disadvantage. Understanding and improving yield is paramount for any manufacturer seeking operational excellence and sustainable growth. Factors influencing yield can range from raw material quality and equipment maintenance to process parameters and operator skill. Optimizing yield requires a holistic approach, encompassing all stages of the production process, from design and procurement to production and quality control. The implications of yield extend across various industries, impacting everything from semiconductor fabrication to pharmaceutical production and even food processing. Analyzing yield data provides crucial insights for continuous improvement initiatives, allowing manufacturers to pinpoint bottlenecks, refine processes, and ultimately, maximize their return on investment.
Overview of this Article
This article will comprehensively explore the multifaceted concept of yield in manufacturing. We will delve into various yield definitions, explore different calculation methods, examine the key factors impacting yield, and provide actionable strategies for improvement. Readers will gain a thorough understanding of yield’s importance, its practical applications, and how to leverage it for enhanced operational efficiency.
Research and Effort Behind the Insights
This article draws upon extensive research, incorporating data from industry reports, academic publications, and insights from manufacturing experts. A structured approach has been employed to ensure accuracy and provide actionable insights for readers across diverse manufacturing sectors.
Key Aspects of Yield in Manufacturing
Key Aspect | Description |
---|---|
Yield Calculation Methods | Various methods exist, including First-Pass Yield, Rolled Throughput Yield, and overall equipment effectiveness (OEE). |
Factors Affecting Yield | Raw material quality, equipment reliability, process parameters, operator skill, and design flaws. |
Yield Improvement Strategies | Process optimization, preventative maintenance, operator training, and advanced quality control techniques. |
Yield Data Analysis | Statistical process control (SPC) and data-driven decision-making to identify and address yield bottlenecks. |
Yield Management Systems | Software and tools for tracking, analyzing, and improving yield across the manufacturing process. |
Let’s dive deeper into the key aspects of yield in manufacturing, starting with a detailed exploration of various yield calculation methods.
1. Yield Calculation Methods
Several methods exist for calculating yield, each offering a unique perspective on manufacturing efficiency. The most common include:
-
First-Pass Yield (FPY): This is the simplest metric, representing the percentage of units successfully produced without defects on the first attempt. It's calculated as (Number of good units produced / Total number of units started) * 100. FPY is useful for identifying immediate process problems but doesn't account for rework or repair.
-
Rolled Throughput Yield (RTY): This is a more comprehensive metric that considers the cumulative effect of defects throughout the entire manufacturing process. It accounts for rework, repair, and scrap, providing a more realistic picture of overall efficiency. RTY is calculated by multiplying the individual yields of each process step. For example, if a process has three steps with yields of 90%, 95%, and 98%, the RTY is 0.90 * 0.95 * 0.98 = 83.58%. This highlights the cumulative impact of even small defects at each stage.
-
Overall Equipment Effectiveness (OEE): OEE is a more holistic measure that considers not only yield but also availability and performance of the equipment. It considers factors like downtime, speed, and quality. OEE helps manufacturers identify areas for improvement beyond just the yield itself, targeting equipment utilization and performance as well. A high OEE indicates efficient equipment usage and high-quality output.
-
Production Yield: This is a broader term encompassing both the quantity and quality of the output. It reflects the percentage of usable products produced relative to the total input. This is a more holistic view of yield, considering both the number of good units and their quality.
The choice of yield calculation method depends on the specific manufacturing process and the information required. Many manufacturers utilize a combination of these methods to gain a comprehensive understanding of their efficiency.
2. Factors Affecting Yield
Several interconnected factors influence manufacturing yield. Understanding these factors is crucial for implementing effective improvement strategies. These include:
-
Raw Material Quality: Inconsistent or defective raw materials are a major contributor to low yield. Strict quality control measures at the procurement stage are essential.
-
Equipment Reliability: Malfunctioning or outdated equipment leads to increased downtime, defects, and ultimately, lower yield. Regular maintenance and timely upgrades are vital.
-
Process Parameters: Incorrect temperature, pressure, speed, or other process parameters can significantly impact product quality and yield. Precise control and optimization are crucial.
-
Operator Skill: Human error can contribute significantly to defects and lower yield. Proper training, clear procedures, and effective supervision are necessary.
-
Design Flaws: Design issues can lead to manufacturing difficulties, increased scrap, and low yield. Thorough design validation and prototyping are essential.
-
Environmental Factors: Temperature fluctuations, humidity, and other environmental factors can impact the manufacturing process and yield. Controlled environments are necessary for sensitive processes.
3. Yield Improvement Strategies
Improving yield requires a multi-pronged approach that addresses all contributing factors. Key strategies include:
-
Process Optimization: This involves identifying and eliminating bottlenecks, streamlining processes, and optimizing parameters to maximize efficiency. Lean manufacturing principles and Six Sigma methodologies can be effectively implemented.
-
Preventative Maintenance: Regular equipment maintenance minimizes downtime and prevents unexpected failures, leading to higher yield. A preventative maintenance schedule should be established and diligently followed.
-
Operator Training: Investing in comprehensive operator training improves skills, reduces errors, and enhances process consistency, contributing to higher yield.
-
Advanced Quality Control: Implementing advanced quality control techniques, such as statistical process control (SPC), helps identify and address process variations before they lead to defects.
-
Supply Chain Management: Ensuring a reliable supply of high-quality raw materials through effective supply chain management is crucial for consistent yield.
-
Data Analysis: Analyzing yield data helps identify trends, patterns, and potential causes of low yield. This data-driven approach allows for targeted improvements.
4. Exploring the Connection Between Defects and Yield
Defects are the primary antagonist of high yield. The number and type of defects directly impact the overall yield rate. Understanding the root causes of defects is essential for effective mitigation. This involves using tools like Failure Mode and Effects Analysis (FMEA) to identify potential failure points and implement preventative measures. Statistical process control (SPC) charts can monitor process variations and identify deviations from acceptable limits, allowing for timely intervention before defects accumulate. The cost of defects extends beyond the direct cost of scrap; it includes rework, downtime, and customer dissatisfaction, impacting overall profitability. Therefore, implementing robust defect prevention strategies is paramount for enhancing yield.
Further Analysis of Defects
Defect Type | Root Causes | Mitigation Strategies | Impact on Yield |
---|---|---|---|
Material Defects | Poor raw material quality, supplier issues | Stricter quality control, supplier audits, alternative sources | Significant |
Process Defects | Incorrect parameters, equipment malfunction | Process optimization, preventative maintenance | Moderate |
Human Error | Lack of training, poor procedures, fatigue | Operator training, improved procedures, ergonomic improvements | Moderate to High |
Design Defects | Design flaws, inadequate testing | Thorough design validation, prototyping, design for manufacturing (DFM) | Significant |
5. Yield Management Systems
Modern manufacturing relies on sophisticated yield management systems – often software-based – to track, analyze, and improve yield across the entire production process. These systems collect data from various sources, including machines, sensors, and quality control systems, providing real-time insights into yield performance. Data analysis capabilities within these systems identify trends, patterns, and potential areas for improvement, allowing for data-driven decision making. Furthermore, these systems can integrate with other enterprise resource planning (ERP) systems, providing a holistic view of manufacturing operations and enabling efficient resource allocation.
6. Frequently Asked Questions (FAQ)
-
Q: What is the difference between first-pass yield and rolled throughput yield?
- A: First-pass yield measures the percentage of good units on the first attempt, ignoring rework. Rolled throughput yield considers the cumulative effect of defects throughout the entire process, providing a more realistic picture of overall efficiency.
-
Q: How can I improve yield in my manufacturing process?
- A: Improving yield requires a multi-pronged approach focusing on process optimization, preventative maintenance, operator training, advanced quality control, and data analysis.
-
Q: What are the key performance indicators (KPIs) for yield?
- A: Key KPIs include first-pass yield, rolled throughput yield, overall equipment effectiveness (OEE), and production yield. The most relevant KPI depends on the specific manufacturing process and goals.
-
Q: How does yield impact profitability?
- A: High yield directly translates to reduced waste, lower costs, and higher profits. Low yield increases costs and reduces profitability.
-
Q: What role does data analysis play in yield improvement?
- A: Data analysis allows manufacturers to identify trends, patterns, and root causes of low yield, enabling targeted improvements and data-driven decision-making.
-
Q: Are there any industry-specific considerations for yield?
- A: Yes, specific industries have unique challenges and best practices for yield optimization. For example, the semiconductor industry has extremely stringent requirements for yield due to high costs per unit.
Practical Tips for Yield Improvement
-
Implement a robust preventative maintenance program: Regularly schedule equipment inspections and repairs to minimize downtime and prevent failures.
-
Invest in operator training: Provide comprehensive training to improve skills, reduce errors, and enhance consistency.
-
Utilize statistical process control (SPC): Monitor process variations and identify deviations to address issues proactively.
-
Analyze yield data regularly: Identify trends, patterns, and root causes of low yield to inform improvement initiatives.
-
Optimize process parameters: Fine-tune process settings to maximize efficiency and minimize defects.
-
Improve raw material quality control: Implement rigorous quality checks to ensure consistent material quality.
-
Employ Lean Manufacturing principles: Identify and eliminate waste in the manufacturing process to improve efficiency.
-
Implement a defect prevention program: Focus on proactive measures to prevent defects from occurring in the first place.
Final Conclusion
Yield in manufacturing is not just a metric; it's a reflection of overall operational efficiency and a crucial indicator of profitability. Understanding various yield calculation methods, identifying factors affecting yield, and implementing effective improvement strategies are essential for any manufacturer striving for excellence. By adopting a data-driven approach, investing in training and technology, and embracing a culture of continuous improvement, manufacturers can significantly enhance their yield, reducing costs, increasing profits, and gaining a competitive edge. The journey to high yield is an ongoing process requiring constant monitoring, analysis, and adaptation. The insights and strategies discussed in this article provide a solid foundation for manufacturers to embark on this journey and reap the significant rewards of improved efficiency and profitability.
Latest Posts
Latest Posts
-
Wells Fargo Cash Wise Credit Card Foreign Transaction Fee
Apr 02, 2025
-
Minimum Payment On Wells Fargo Active Cash Card
Apr 02, 2025
-
Minimum Amount Of Federal Withholding
Apr 02, 2025
-
Federal Withholding Ohio
Apr 02, 2025
-
Federal Tax Ohio
Apr 02, 2025
Related Post
Thank you for visiting our website which covers about Yield Definition In Manufacturing . We hope the information provided has been useful to you. Feel free to contact us if you have any questions or need further assistance. See you next time and don't miss to bookmark.