Xrt Means
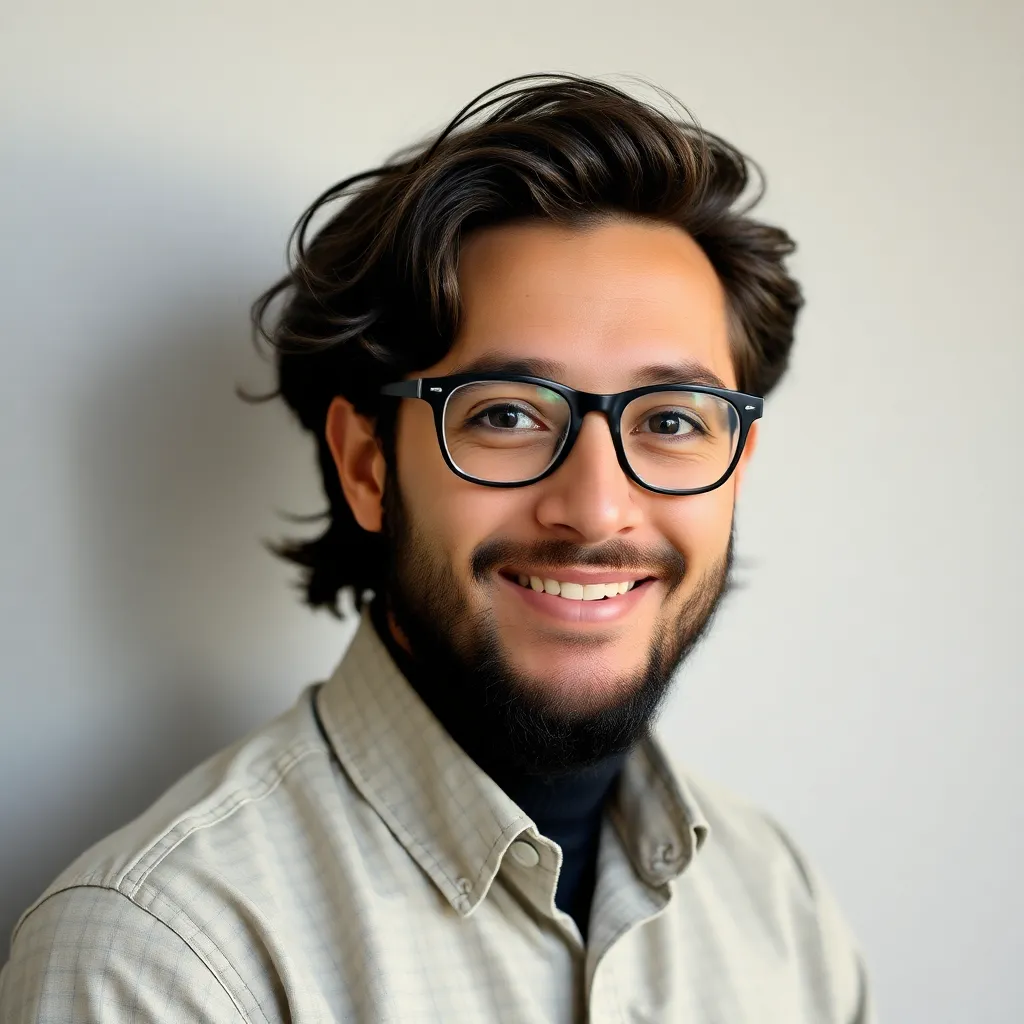
adminse
Mar 29, 2025 · 10 min read

Table of Contents
Decoding XRT: Unveiling the Mysteries of X-ray Reflectivity
What makes X-ray reflectivity a groundbreaking technique in materials science?
X-ray reflectivity (XRR) is revolutionizing materials characterization, offering unparalleled insights into thin film structures and surface properties.
Editor’s Note: This comprehensive guide to X-ray reflectivity (XRR) has been published today.
Why X-ray Reflectivity Matters
X-ray reflectivity (XRR), often simply called XRR, is a non-destructive surface-sensitive technique that provides detailed information about the structure and composition of thin films and surfaces. Its importance stems from its ability to characterize materials at the nanometer scale, a level of detail crucial for many modern technological applications. From semiconductor manufacturing to the development of advanced coatings, XRR provides critical data for quality control, process optimization, and fundamental research. The technique is particularly relevant in industries dealing with thin films, layered structures, and surface modifications, impacting fields such as microelectronics, optics, and biotechnology. Understanding XRR is becoming increasingly important for researchers and engineers seeking to optimize material properties and develop innovative technologies. This heightened relevance stems from the growing demand for precise control over nanoscale structures, driving the development of more sophisticated and accurate characterization methods. The increasing complexity of modern materials also calls for advanced analysis methods capable of distinguishing subtle differences in composition and structure.
Overview of the Article
This article offers a comprehensive exploration of X-ray reflectivity, covering its fundamental principles, experimental setup, data analysis, and diverse applications. Readers will gain a thorough understanding of how XRR works, what information it provides, and its significance in various scientific and industrial domains. The article will also delve into practical considerations, including sample preparation and limitations of the technique. Ultimately, readers will gain a deep appreciation for XRR's role as a powerful tool for materials characterization.
Research and Effort Behind the Insights
This article draws upon extensive research from peer-reviewed scientific publications, technical manuals, and industry reports. The information presented is based on established scientific principles and validated experimental techniques. The analysis integrates theoretical concepts with real-world applications, providing a balanced perspective on the capabilities and limitations of XRR.
Key Takeaways
Key Aspect | Description |
---|---|
Fundamental Principle | X-rays interfere upon reflection from layered structures, yielding information about layer thickness and density. |
Data Analysis | Analysis involves fitting theoretical models to experimental data to extract structural parameters. |
Applications | Semiconductor fabrication, coatings, polymers, biological membranes, and more. |
Advantages | Non-destructive, high sensitivity, nanometer-scale resolution. |
Limitations | Surface roughness effects, limited penetration depth. |
Smooth Transition to Core Discussion
Let’s delve into the core principles of X-ray reflectivity, starting with the fundamental physics behind the technique and progressing to its practical applications in diverse scientific and industrial fields.
Exploring the Key Aspects of XRT
-
XRR Principles: XRR exploits the interference phenomenon of X-rays reflected from a layered structure. When a monochromatic X-ray beam strikes a surface at a glancing angle, it is partially reflected at each interface between layers of different electron densities. These reflected waves interfere constructively or destructively, depending on the path length difference. This interference pattern, recorded as a function of the incident angle, produces characteristic oscillations known as Kiessig fringes, which are directly related to the layer thicknesses. The intensity of the reflected beam provides information about the electron density profile of the sample. This is often used to determine the thickness and density of individual layers, roughness at interfaces, and overall surface roughness.
-
Experimental Setup: A typical XRR experiment involves a monochromatic X-ray source (often a synchrotron or laboratory-based source), a sample stage with precise angular control, and a detector to measure the intensity of the reflected X-rays. The sample is aligned to ensure that the incident X-ray beam grazes the surface. The angle of incidence is then systematically varied, recording the intensity of the reflected X-rays at each angle. The precise alignment and angular control are crucial for obtaining high-quality data. Furthermore, the choice of X-ray wavelength influences the penetration depth and the sensitivity to different features of the sample structure. Different X-ray sources may be needed to optimize for certain applications or material types.
-
Data Analysis and Modeling: Raw XRR data consists of reflectivity as a function of the incident angle. These data are not directly interpretable; instead, they need to be analyzed using specialized software packages that employ numerical modeling techniques. The software fits a theoretical model to the experimental data. This theoretical model includes parameters such as layer thicknesses, electron densities, and interfacial roughnesses. By adjusting these parameters, the software attempts to match the theoretical reflectivity curve to the experimental one. The best fit provides the most accurate values for the structural parameters of the sample. The fitting process requires considerable expertise and experience, and the choice of the model is critical for obtaining accurate results.
-
Applications in Materials Science: XRR's applications span various materials science domains. In semiconductor technology, it is crucial for characterizing thin film transistors, evaluating the quality of deposited dielectric layers, and studying the interfaces between different materials. In the coatings industry, XRR helps determine the thickness and uniformity of protective coatings, determining their durability and performance. The technique is also applicable in the study of polymers, where it provides information about layer thickness, density, and interfacial interactions. In the field of biology, XRR has been used to investigate biological membranes, providing insights into their structure and dynamics. This wide range of applications underscores the versatility and power of XRR as a materials characterization technique.
-
Advanced Techniques and Extensions: Beyond basic XRR, several advanced techniques have been developed to extend its capabilities. These include grazing incidence small-angle X-ray scattering (GISAXS), which provides information about lateral structures within thin films, and resonant X-ray reflectivity (R XR), which is sensitive to the chemical state of the elements within the sample. These extensions enhance the analytical depth and make XRR applicable to a broader range of materials and questions.
-
Limitations of XRR: While a powerful technique, XRR has some limitations. Its sensitivity to surface roughness can complicate data analysis and may require advanced modeling techniques. The penetration depth of X-rays is limited, making it primarily a surface-sensitive technique. It might not be appropriate for characterizing very thick samples or samples with highly absorbing components. The data analysis can be complex and requires expertise in modeling and fitting algorithms. Despite these limitations, XRR remains a widely used and invaluable tool in materials science.
Closing Insights
X-ray reflectivity is not merely a laboratory technique; it is a critical component of many industrial processes and scientific discoveries. Its capacity to provide high-resolution structural information on thin films and surface layers has profound implications across various fields. The technique's versatility, combined with continuous advancements in instrumentation and data analysis, ensures its continued importance in materials science. Its application in areas such as semiconductor technology, the development of advanced coatings, and the understanding of biological membranes underscores its enduring relevance. The detailed structural information provided by XRR remains crucial for both understanding fundamental material properties and controlling manufacturing processes.
Exploring the Connection Between Surface Roughness and XRR
Surface roughness significantly impacts the accuracy and interpretation of XRR data. Rough surfaces scatter X-rays more diffusely, leading to a reduction in the intensity of specularly reflected X-rays and potentially obscuring the characteristic Kiessig fringes. The degree of roughness affects the quality of the data and the accuracy of the extracted structural parameters. In severe cases, surface roughness can make it impossible to reliably determine layer thicknesses or densities. Mitigation strategies include careful sample preparation and the use of advanced modeling techniques that incorporate surface roughness effects. The impact of roughness is not merely a source of error; it is also a parameter that can be quantified by XRR. This allows for the study of the surface morphology and its effect on material performance. Detailed analysis can reveal correlation between surface roughness, processing conditions, and final material properties, improving process optimization and quality control.
Further Analysis of Surface Roughness
Surface roughness is usually characterized by its root-mean-square (RMS) value, representing the average deviation from a perfectly smooth surface. The effect of roughness can be modeled within the XRR data analysis, taking into account the distribution of surface heights. This often involves using a Nevot-Croce model or similar approaches that incorporate a roughness parameter into the theoretical reflectivity calculation. The choice of model depends on the nature of the roughness (e.g., Gaussian, exponential). The resulting RMS roughness value is an important parameter in determining the quality of a thin film or surface. In certain applications, a smooth surface is essential for optimal performance, while in other cases, controlled surface roughness is beneficial. XRR analysis is pivotal in understanding and controlling these characteristics.
FAQ Section
-
Q: What is the typical X-ray wavelength used in XRR? A: The optimal wavelength depends on the material and the desired penetration depth, but wavelengths in the range of 0.154 nm (Cu Kα radiation) are commonly used.
-
Q: How does XRR compare to other surface characterization techniques? A: XRR provides unique information about layer thickness and density with nanometer-scale resolution, complementing techniques like AFM and ellipsometry.
-
Q: Can XRR be used for liquid samples? A: While challenging, specialized setups allow for XRR measurements on liquid surfaces and interfaces.
-
Q: What are the limitations of the model fitting in XRR data analysis? A: Model fitting can be complex, sensitive to initial parameters, and might be subject to non-uniqueness if the model is too simple.
-
Q: How can I prepare my sample for XRR measurements? A: Sample preparation is crucial. The surface must be clean and flat. Specific methods depend on the material and the goals of the study.
-
Q: What are the typical costs associated with XRR measurements? A: Costs vary depending on the facility, the duration of the measurement, and any specialized sample preparation required.
Practical Tips
-
Optimize Sample Preparation: Ensure a clean, flat surface to minimize scattering and improve data quality.
-
Careful Alignment: Precise alignment is crucial for accurate measurements.
-
Choose Appropriate X-ray Wavelength: Select a wavelength that optimizes penetration depth and sensitivity to the features of interest.
-
Use Appropriate Models: Select a model fitting process that accurately reflects the expected sample structure and roughness.
-
Validate Results: Cross-validate results with other characterization techniques whenever possible.
-
Consult with Experts: Seek guidance from experts in XRR for complex samples or challenging applications.
-
Understand Limitations: Be aware of the limitations of the technique and interpret results carefully.
-
Maintain Data Quality: Proper experimental design and data acquisition procedures are critical for high-quality data.
Final Conclusion
X-ray reflectivity (XRR) stands as a powerful and versatile technique with far-reaching implications across numerous scientific and industrial fields. Its capacity to provide detailed structural information at the nanometer scale has revolutionized the characterization of thin films and surfaces. By understanding the fundamental principles, experimental techniques, and data analysis methods, researchers and engineers can leverage XRR to solve critical challenges and drive innovation in material science and technology. The information presented in this article offers a solid foundation for those looking to apply or understand this vital technique. Further exploration into specific applications and advanced techniques will reveal the extensive possibilities of XRR.
Latest Posts
Latest Posts
-
What Is The Best Budget Book
Apr 03, 2025
-
What Is The Best Book On Money Management
Apr 03, 2025
-
Money Management Trading Future
Apr 03, 2025
-
Why Money Management Is Important In Trading
Apr 03, 2025
-
Trading Money Management Strategies
Apr 03, 2025
Related Post
Thank you for visiting our website which covers about Xrt Means . We hope the information provided has been useful to you. Feel free to contact us if you have any questions or need further assistance. See you next time and don't miss to bookmark.