Work Practice Control Definition
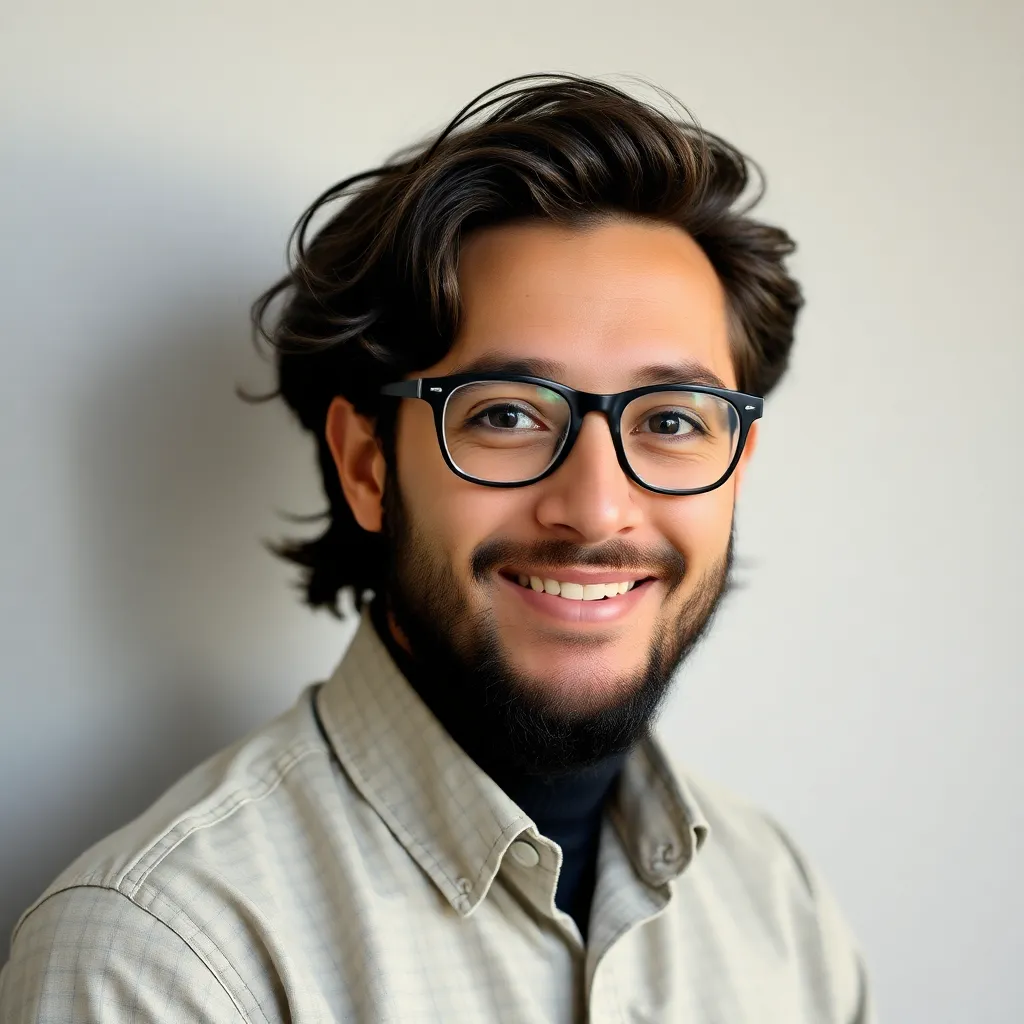
adminse
Mar 29, 2025 · 8 min read

Table of Contents
Mastering Work Practice Controls: A Comprehensive Guide to Definition, Implementation, and Best Practices
What defines effective work practice controls, and why are they crucial for a safe and productive workplace?
Work practice controls are the cornerstone of a robust safety management system, directly impacting employee well-being and organizational success.
Editor’s Note: This comprehensive guide to work practice controls has been published today, offering the latest insights and best practices for implementing and maintaining effective safety protocols.
Why Work Practice Controls Matter
Work practice controls encompass the methods and procedures used to ensure that tasks are performed safely and efficiently. They go beyond simply providing personal protective equipment (PPE) or engineering controls; instead, they focus on changing how a job is done to minimize risks. This proactive approach significantly reduces the likelihood of workplace incidents, fostering a culture of safety and boosting productivity. The importance of work practice controls extends to various sectors, including manufacturing, healthcare, construction, and technology, impacting employee health, legal compliance, and the overall bottom line. Effective work practice controls can prevent injuries, illnesses, and property damage, resulting in reduced workers' compensation claims, improved employee morale, and enhanced operational efficiency. Moreover, strong work practice controls contribute to a positive company image and demonstrate a commitment to employee well-being, which can attract and retain talent. In the context of regulatory compliance, effective implementation of these controls is crucial for avoiding penalties and maintaining a positive relationship with regulatory bodies.
Overview of This Article
This article delves into the intricacies of work practice controls, exploring their definition, implementation strategies, and real-world applications. Readers will gain a comprehensive understanding of how to develop, implement, and maintain effective work practice controls, ultimately contributing to a safer and more productive work environment. The article will cover the foundational principles of work practice controls, highlight various implementation methods, explore the connection between work practice controls and other safety measures, address common challenges and solutions, and provide actionable steps for creating a robust safety management system.
Research and Effort Behind the Insights
The information presented in this article is based on extensive research, incorporating data from leading safety organizations like OSHA (Occupational Safety and Health Administration), NIOSH (National Institute for Occupational Safety and Health), and industry best practices. This includes reviewing numerous case studies, safety manuals, regulatory guidelines, and expert opinions to ensure accuracy and relevance. The insights provided are data-driven and designed to be practical and immediately applicable to a variety of workplace settings.
Key Takeaways
Key Aspect | Description |
---|---|
Definition of Work Practice Controls | Procedures and methods to perform tasks safely; focus on modifying work methods, not just providing PPE or engineering controls. |
Implementation Strategies | Training, standard operating procedures (SOPs), audits, communication, regular review and updates, leadership commitment. |
Importance of Training | Crucial for effective implementation; ensures employees understand and can apply the controls. |
Role of Supervision | Essential for monitoring compliance, providing feedback, and addressing deviations from established procedures. |
Continuous Improvement | Regularly review and update controls based on incident investigations, audits, and best practices. |
Legal and Regulatory Compliance | Adherence to relevant OSHA, NIOSH, and other applicable safety regulations. |
Smooth Transition to Core Discussion
Having established the fundamental importance of work practice controls, let's now delve into a deeper exploration of their key aspects. We will analyze the core elements involved in designing, implementing, and maintaining an effective work practice control program.
Exploring the Key Aspects of Work Practice Controls
-
Defining Safe Work Practices: This involves clearly identifying potential hazards associated with specific tasks and developing detailed procedures to mitigate those risks. It's essential to involve employees in this process to gain valuable insights and ensure buy-in.
-
Developing Standard Operating Procedures (SOPs): SOPs provide step-by-step instructions for performing tasks safely. They should be concise, easy to understand, and readily accessible to all employees. Visual aids, such as diagrams and flowcharts, can improve comprehension.
-
Implementing Effective Training Programs: Thorough training is paramount. Employees must understand the rationale behind the work practice controls, the procedures they need to follow, and the consequences of non-compliance. Regular refresher training ensures ongoing competency.
-
Establishing Monitoring and Evaluation Systems: Regular audits and inspections are critical to ensure compliance with established procedures. Feedback mechanisms allow employees to report potential hazards and suggest improvements. Data collected from these systems should be used to continuously improve the effectiveness of the controls.
-
Addressing Non-Compliance: A clear process for addressing non-compliance is essential. This might involve corrective actions, retraining, or disciplinary measures, depending on the severity of the violation. The focus should be on education and improvement, not punishment.
-
Continuous Improvement and Refinement: Work practice controls are not static; they must be regularly reviewed and updated to reflect changes in technology, processes, and best practices. Incident investigations provide valuable insights for identifying areas needing improvement.
Closing Insights
Effective work practice controls are not merely a checklist; they are an integral part of a proactive safety culture. By implementing a comprehensive program that includes clear procedures, thorough training, regular monitoring, and a commitment to continuous improvement, organizations can significantly reduce workplace risks, protect their employees, and enhance overall productivity. The benefits extend far beyond compliance; they contribute to a safer, more efficient, and ultimately more successful organization.
Exploring the Connection Between Ergonomics and Work Practice Controls
Ergonomics, the science of designing workspaces and tasks to fit the capabilities of the human body, is intrinsically linked to work practice controls. Poor ergonomics can lead to musculoskeletal disorders (MSDs), such as carpal tunnel syndrome and back pain. Work practice controls play a vital role in mitigating these risks by promoting proper posture, lifting techniques, and workstation design. For instance, a work practice control might specify the use of ergonomic tools, chairs, and lifting aids, coupled with training on proper lifting techniques and workstation setup. Failure to address ergonomic factors within work practice controls can negate the positive effects of other safety measures. Regular ergonomic assessments, combined with the implementation of ergonomic work practices, are crucial for preventing MSDs and ensuring a healthy work environment. Analyzing tasks for repetitive motions, awkward postures, and excessive force is key to identifying and mitigating ergonomic risks.
Further Analysis of Ergonomics in Work Practice Controls
Ergonomic Factor | Impact on Work Practice Controls | Mitigation Strategies |
---|---|---|
Repetitive Movements | Can lead to MSDs; controls should limit repetitive actions and introduce micro-breaks. | Job rotation, workstation redesign, use of automated tools, paced work strategies. |
Awkward Postures | Strains muscles and joints; controls should promote neutral postures. | Adjustable workstations, ergonomic tools, proper lifting techniques, training on posture. |
Excessive Force | Overstrains muscles; controls should minimize the amount of force required for tasks. | Ergonomic tools, powered equipment, assistance devices, job redesign, task analysis. |
Vibration | Can cause hand-arm vibration syndrome (HAVS); controls should limit exposure to vibration. | Use of anti-vibration gloves, tools, and equipment, regular breaks, medical surveillance. |
Prolonged Static Postures | Can lead to fatigue and MSDs; controls should encourage movement and breaks. | Frequent breaks, workstation adjustments, stretching exercises, job rotation, standing desks. |
FAQ Section
-
Q: What is the difference between work practice controls and engineering controls? A: Engineering controls address hazards at the source, modifying equipment or processes. Work practice controls modify how the work is done.
-
Q: Who is responsible for implementing work practice controls? A: Management is ultimately responsible, but employee involvement is crucial for successful implementation.
-
Q: How often should work practice controls be reviewed? A: Regularly, at least annually, or more frequently if there are changes in processes or technology.
-
Q: What happens if an employee doesn't follow a work practice control? A: This depends on the severity and the company's policies; it could range from retraining to disciplinary action.
-
Q: Are work practice controls legally required? A: Yes, many jurisdictions have regulations requiring employers to implement appropriate safety controls, including work practice controls.
-
Q: How can I get help developing work practice controls? A: Consult with safety professionals, OSHA, NIOSH, and other relevant resources.
Practical Tips for Implementing Work Practice Controls
- Conduct a thorough hazard assessment: Identify all potential hazards related to each job.
- Develop clear and concise SOPs: Use simple language and visual aids.
- Provide comprehensive training: Ensure employees understand and can apply the controls.
- Implement a system for monitoring compliance: Conduct regular audits and inspections.
- Establish a process for addressing non-compliance: Address issues promptly and fairly.
- Review and update controls regularly: Stay current with best practices and regulatory changes.
- Encourage employee participation: Involve employees in the development and implementation process.
- Use data to track effectiveness: Monitor injury rates and other relevant metrics.
Final Conclusion
Work practice controls are a fundamental element of a robust safety management system. By understanding their definition, implementing effective strategies, and continuously refining processes, organizations can foster a culture of safety, reduce workplace hazards, and protect their most valuable asset: their employees. The proactive approach embodied in work practice controls goes beyond mere compliance; it reflects a commitment to creating a healthy, productive, and thriving work environment. Continuous improvement and ongoing employee engagement are key to maintaining a program's effectiveness and ensuring long-term success. The journey towards a safer workplace is an ongoing process that requires consistent effort and commitment from all stakeholders.
Latest Posts
Latest Posts
-
Top 10 Money Management Books
Apr 03, 2025
-
What Is The Best Book On Financial Management
Apr 03, 2025
-
What Is The Best Budget Book
Apr 03, 2025
-
What Is The Best Book On Money Management
Apr 03, 2025
-
Money Management Trading Future
Apr 03, 2025
Related Post
Thank you for visiting our website which covers about Work Practice Control Definition . We hope the information provided has been useful to you. Feel free to contact us if you have any questions or need further assistance. See you next time and don't miss to bookmark.