What Are Workplace Controls
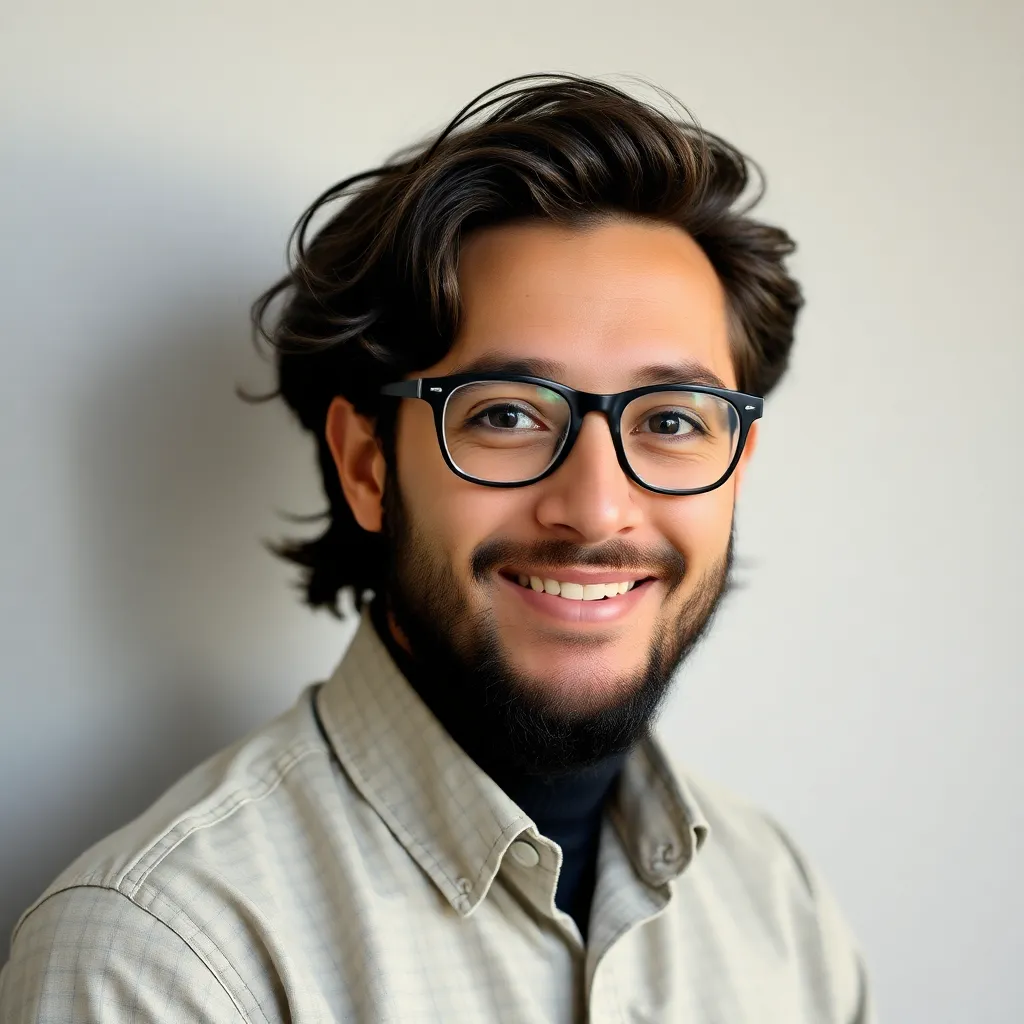
adminse
Mar 29, 2025 · 10 min read

Table of Contents
Unlocking Workplace Safety: A Comprehensive Guide to Workplace Controls
What makes a truly safe workplace? Is it just the absence of accidents, or something more proactive and preventative?
Workplace controls are the cornerstone of a safe and productive environment, proactively mitigating risks and fostering a culture of safety.
Editor’s Note: This comprehensive guide to workplace controls has been published today, offering up-to-date insights and practical advice for creating safer workplaces.
Why Workplace Controls Matter
Workplace safety isn't merely a legal requirement; it's a fundamental ethical responsibility. A safe workplace protects employees' physical and mental well-being, reduces the risk of costly accidents and lost productivity, improves employee morale and engagement, and enhances a company's reputation. Effective workplace controls are the linchpin of achieving this safety-first culture. They are integral to compliance with OSHA (Occupational Safety and Health Administration) regulations and similar international standards, minimizing liability and potential legal ramifications. The economic benefits alone, stemming from reduced workers' compensation claims and increased efficiency, make investing in robust control measures a strategic imperative for any organization. Beyond the economic impact, a safer work environment fosters a sense of trust and respect, contributing to a more positive and productive work culture.
Overview of this Article
This article delves into the multifaceted world of workplace controls, exploring their hierarchy, various types, implementation strategies, and ongoing maintenance. Readers will gain a comprehensive understanding of how to identify hazards, select appropriate control measures, and establish a culture of proactive risk management. We will examine best practices, real-world examples, and address common misconceptions surrounding workplace control implementation.
Research and Effort Behind the Insights
This article draws upon extensive research, including analysis of OSHA guidelines, industry best practices, and case studies from diverse sectors. It incorporates insights from leading safety professionals and integrates data-driven evidence to ensure accuracy and provide actionable guidance.
Key Takeaways
Key Aspect | Description |
---|---|
Hierarchy of Controls | Prioritizes elimination, substitution, engineering, administrative, and PPE controls. |
Types of Workplace Controls | Engineering, Administrative, and Personal Protective Equipment (PPE). |
Hazard Identification | Crucial first step involving risk assessments and job hazard analyses (JHAs). |
Implementation & Training | Thorough training and communication are vital for effective control implementation. |
Monitoring & Evaluation | Regular inspections, audits, and incident investigations are essential for ongoing effectiveness. |
Legal and Regulatory Compliance | Adherence to OSHA and other relevant regulations is paramount. |
Smooth Transition to Core Discussion:
Now, let's explore the key aspects of workplace controls in detail, starting with the fundamental hierarchy that guides their selection and implementation.
Exploring the Key Aspects of Workplace Controls
-
The Hierarchy of Controls: This fundamental principle dictates the order of preference when selecting control measures. The goal is to eliminate hazards whenever possible, progressing through increasingly less effective controls only if elimination isn't feasible. The hierarchy typically follows this order:
-
Elimination: The most effective control, completely removing the hazard from the workplace. This might involve redesigning a process, substituting a hazardous material, or relocating a dangerous operation.
-
Substitution: Replacing a hazardous substance or process with a safer alternative. For example, replacing a solvent with a water-based cleaner or using automated equipment to reduce manual handling.
-
Engineering Controls: Implementing physical changes to the workplace to reduce or eliminate hazards. Examples include installing machine guards, implementing ventilation systems, using noise-dampening materials, or providing ergonomic workstations.
-
Administrative Controls: Changes to work practices, procedures, and policies to minimize risk. This includes job rotation, providing training, implementing safety protocols, establishing clear communication channels, and implementing a robust safety management system.
-
Personal Protective Equipment (PPE): The least effective control, used as a last resort when other controls aren't feasible or sufficient. PPE includes safety glasses, gloves, hard hats, respirators, and hearing protection. It's crucial to remember that PPE protects the individual, not the hazard.
-
-
Engineering Controls in Detail: These are often the most effective and sustainable solutions. They modify the work environment itself, reducing the likelihood of exposure to hazards. Examples include:
- Machine Guarding: Preventing access to moving parts of machinery.
- Ventilation Systems: Reducing exposure to airborne contaminants.
- Local Exhaust Ventilation (LEV): Capturing hazardous fumes and dust at their source.
- Ergonomic Design: Creating workstations that reduce strain and injury.
- Emergency Shut-off Systems: Allowing for quick cessation of hazardous operations.
-
Administrative Controls: A Deeper Dive: These controls focus on changing the way work is done. Their effectiveness depends heavily on employee training, clear communication, and consistent enforcement. Examples include:
- Job Hazard Analysis (JHA): A systematic process to identify and assess hazards associated with specific tasks.
- Lockout/Tagout Procedures: Preventing accidental release of energy during maintenance or repair.
- Safe Work Permits: Authorizing specific high-risk activities under controlled conditions.
- Training Programs: Educating employees about hazards and safe work practices.
- Regular Safety Inspections: Identifying potential hazards before they cause incidents.
-
Personal Protective Equipment (PPE): Limitations and Best Practices: While PPE is crucial, it should always be considered the last line of defense. Its effectiveness depends on proper selection, training, maintenance, and consistent use. Important considerations include:
- Proper Selection: Choosing the right PPE for the specific hazard.
- Fit Testing: Ensuring proper fit for respirators and other equipment.
- Training and Education: Instructing employees on proper use and limitations of PPE.
- Maintenance and Replacement: Regularly inspecting and replacing worn or damaged equipment.
- Compliance with Standards: Selecting PPE that meets relevant industry standards.
-
Implementing and Maintaining Workplace Controls: Successful implementation requires a multi-faceted approach:
- Hazard Identification and Risk Assessment: Conducting thorough risk assessments to pinpoint hazards and evaluate their severity and likelihood.
- Control Selection: Choosing the most effective control measures based on the hierarchy.
- Implementation and Training: Providing comprehensive training to employees on the use and effectiveness of the chosen controls.
- Monitoring and Evaluation: Regularly inspecting the workplace to ensure controls remain effective and identifying areas for improvement.
- Record Keeping: Maintaining accurate records of hazards, controls, training, and incidents.
-
Legal and Regulatory Compliance: Workplace controls must comply with relevant legislation and regulations, such as OSHA standards in the US or equivalent regulations in other countries. Non-compliance can result in significant fines, legal action, and reputational damage. Staying updated on changes in legislation and incorporating them into safety programs is crucial.
Closing Insights
Effective workplace controls are not a one-time implementation but an ongoing process of identification, assessment, control, monitoring, and improvement. A proactive approach, prioritizing hazard elimination and substitution whenever possible, is essential. By integrating a strong safety culture, robust training programs, and regular inspections, organizations can minimize risks, protect their employees, and cultivate a more productive and positive work environment. The investment in comprehensive workplace controls is not merely a cost; it is a strategic investment in the well-being of the workforce and the long-term success of the organization. The successful implementation of workplace controls translates directly to a reduction in workplace incidents, lower insurance premiums, increased productivity, and a significant enhancement to a company's overall reputation. Failing to implement these controls carries far-reaching consequences, ranging from financial penalties and legal liabilities to the devastating human cost of preventable injuries and fatalities.
Exploring the Connection Between Training and Workplace Controls
Effective training is not merely an adjunct to workplace controls; it's an integral component of their success. Training empowers employees to understand, use, and maintain the implemented controls. Without adequate training, even the most sophisticated engineering controls can be rendered ineffective. For example, a perfectly functioning machine guard is useless if employees don't understand its purpose or how to use it correctly. Training should encompass:
- Hazard Recognition: Identifying potential hazards in the workplace.
- Control Understanding: Learning how the implemented controls mitigate those hazards.
- Safe Work Practices: Understanding and adhering to standard operating procedures (SOPs).
- Emergency Procedures: Knowing how to respond in case of an accident or emergency.
- PPE Use: Proper selection, fitting, use, and maintenance of personal protective equipment.
Roles: The role of supervisors is crucial in ensuring that employees receive adequate training and understand the importance of following safety protocols. Safety professionals and managers are responsible for developing and delivering training programs, regularly evaluating their effectiveness, and ensuring compliance.
Real-World Examples: A manufacturing plant that implemented a new machine guarding system also provided extensive training to employees on its safe operation, dramatically reducing the number of hand injuries. Conversely, a construction site with excellent safety equipment but inadequate training saw a high rate of accidents.
Risks and Mitigations: Inadequate training poses significant risks, including accidents, injuries, non-compliance with regulations, and damage to company reputation. Regular refresher training, competency assessments, and clear communication are key mitigations.
Impact and Implications: Effective training leads to increased safety awareness, improved compliance, reduced accidents, and a more engaged and productive workforce. Conversely, insufficient training can have devastating consequences, impacting employees' well-being, productivity, and the company's bottom line.
Further Analysis of Training
Training effectiveness can be measured through various methods, including:
- Pre- and Post-Training Assessments: Measuring knowledge gained.
- Observation of Work Practices: Assessing adherence to safe work procedures.
- Incident Reporting: Tracking accident rates and identifying areas for improvement in training.
- Employee Feedback: Gathering input on training effectiveness and making improvements.
A well-structured training program should be tailored to the specific hazards and controls in the workplace, using multiple learning methods (e.g., classroom instruction, hands-on practice, simulations) to enhance comprehension and retention.
FAQ Section
-
Q: What happens if a workplace control fails? A: Immediate action is required. Isolate the hazard, investigate the cause of failure, repair or replace the control, and review the overall safety program.
-
Q: Who is responsible for implementing workplace controls? A: Employers are legally responsible for providing a safe workplace and implementing appropriate controls. However, employee participation and commitment are crucial for success.
-
Q: How often should workplace controls be reviewed? A: Regular reviews (at least annually) are essential, along with reviews following incidents, changes in processes, or introduction of new equipment.
-
Q: What are the penalties for non-compliance with workplace control regulations? A: Penalties vary widely depending on jurisdiction but can include fines, legal action, and reputational damage.
-
Q: How can I know what controls are needed for my specific workplace? A: Conduct a thorough risk assessment, involving employees in the process, to identify hazards and select appropriate control measures based on the hierarchy.
-
Q: What role do employees play in workplace controls? A: Employees are vital. They should be actively involved in identifying hazards, using controls correctly, and reporting any issues.
Practical Tips
- Conduct a thorough risk assessment: Identify all potential hazards in your workplace.
- Prioritize control selection: Follow the hierarchy of controls, starting with elimination and substitution.
- Develop and implement clear procedures: Ensure everyone knows how to use the controls effectively.
- Provide comprehensive training: Educate employees on hazards, controls, and safe work practices.
- Establish a robust reporting system: Encourage employees to report any hazards or control failures promptly.
- Regularly inspect and maintain controls: Ensure ongoing effectiveness and identify any deficiencies.
- Document everything: Maintain records of risk assessments, control measures, training, and inspections.
- Continuously improve: Regularly review your safety program and implement changes based on experience and new information.
Final Conclusion
Workplace controls are not merely a set of regulations; they are the foundation of a safe, productive, and ethical workplace. By understanding the hierarchy of controls, selecting appropriate measures, and fostering a culture of safety, organizations can significantly reduce risks, protect their employees, and build a more successful and sustainable business. The effort invested in establishing and maintaining a robust system of workplace controls represents an investment in people, productivity, and the long-term prosperity of the organization. The commitment to workplace safety is not a cost, but an invaluable investment in the future.
Latest Posts
Latest Posts
-
What Is The Best Book On Financial Management
Apr 03, 2025
-
What Is The Best Budget Book
Apr 03, 2025
-
What Is The Best Book On Money Management
Apr 03, 2025
-
Money Management Trading Future
Apr 03, 2025
-
Why Money Management Is Important In Trading
Apr 03, 2025
Related Post
Thank you for visiting our website which covers about What Are Workplace Controls . We hope the information provided has been useful to you. Feel free to contact us if you have any questions or need further assistance. See you next time and don't miss to bookmark.